-
Call
-
Whatsapp
9825014048
-
Location
Blog
BLOG
Moisture separator maintenance
Moisture separators are indispensable components in compressed air and gas systems, safeguarding downstream equipment and processes from the damaging effects of moisture. However, to maintain their efficiency and reliability, regular maintenance is essential.
In this guide, we’ll explore the importance of moisture separator maintenance and provide practical tips to ensure optimal performance and longevity.
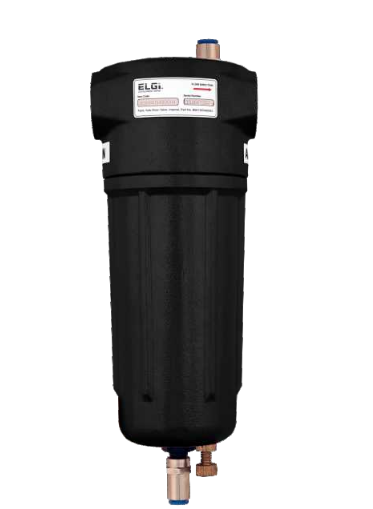
Understanding the Role of Moisture Separators:
Before delving into maintenance, let’s briefly review the function of moisture separators. These devices are designed to remove liquid water droplets and moisture vapour from compressed air and gas streams. By capturing moisture they prevent corrosion, protect equipment and ensure the purity of downstream processes. However, over time, moisture separators can become less effective if not properly maintained.
Importance of moisture separator maintenance:
Proper maintenance of moisture separators is crucial for several reasons:
1. Optimal Performance: Regular maintenance helps ensure that moisture separators operate at peak efficiency, maintaining their ability to remove moisture from compressed air and gas streams effectively.
2. Equipment Protection: By preventing moisture ingress, well-maintained moisture separators help protect downstream equipment from corrosion, contamination, and premature failure.
3. Energy Efficiency: Clean and properly functioning moisture separators contribute to energy savings by reducing the load on downstream equipment and minimizing pressure drop across the system.
4. Process Reliability: Reliable moisture separation is essential for maintaining the integrating and quality of processes that rely on clean and dry compressed air and gas.
Moisture Separator Maintenance Tips:
Now, let’s explore practical maintenance tips to ensure optimal performance of moisture separators:
1. Regular Inspections: Conduct visual inspections of moisture separators to check for signs of damage, corrosion, or blockages. Inspects inlet and outlet connections, drains valves, and internal components for any abnormalities.
2. Drainage Maintenance: Ensure that drain valves are functioning correctly and are free from obstructions. Regularly drain accumulated condensate from the moisture separator to prevent water buildup and potential system damage.
3. Filter Replacement: If your moisture separator is equipped with filters, follow the replacement schedule that is suggested by the manufacturer. Airflow and separation efficiency can be negatively affected by dirty or clogged filters.
4. Cleaning: Periodically clean the internal surfaces of moisture separators to remove any accumulated debris or contaminants. Use mild detergents or solvents as recommended by the manufacturer, and ensure thorough rinsing to prevent residue buildup.
5. Pressure Testing: Conduct pressure tests periodically to check for leaks or integrity issues in the moisture separator. Address any leaks promptly to maintain system efficiency and prevent potential safety hazards.
6. Documentations and Records: Keep detailed records of maintenance activities, including inspection dates, filter replacements, cleaning schedules, and any repairs performed. This documentation can help track maintenance intervals and identify potential issues before they escalate.
7. Professional Service: For complex maintenance tasks or if you encounter any issues beyond your expertise, speak with a trained professional who focuses in gas and compressed air systems.
Conclusion:
In the realm of compressed air and gas systems, moisture separators play a critical role in maintaining system integrity and process reliability. By implementing regular maintenance practices, you can ensure that your moisture separators continue to operate efficiently, protecting downstream equipment and processes from the detrimental effects of moisture contamination. Remember, investing in maintenance today can lead to significant savings and operational benefits in the long run.
FAQs
Frequently Ask Questions
Maintenance is essential to ensure that moisture separators operate at peak efficiency, preventing moisture ingress and protecting downstream equipment from corrosion and contamination.
The frequency of inspections for moisture separators should be determined by parameters like operational conditions, system usage, and manufacturer recommendations. Typically, visual inspections are conducted monthly or quarterly, with more thorough inspections performed annually.
Signs of potential maintenance issues include visible corrosion or damage, reduced separation efficiency, increased pressure drop across the separator, and malfunctioning drain valves. In order to avoid harming the system, any irregularities should be handled quickly.
Drain valves should be checked regularly to ensure proper operation and freedom from obstructions. Accumulated condensate should be drained from the moisture separator at regular intervals to prevent water buildup and potential system damage.
Not all moisture separators are equipped with filters, but for those that are, regular filter replacement is essential to maintain optimal performance. Airflow and separation efficiency can be negatively affected by dirty or clogged filters.
Yes, moisture separators can be cleaned internally to remove accumulated debris or contaminants. Mild detergents or solvents recommended by the manufacturer should be used, followed by thorough rinsing to prevent residue buildup.
Conducting pressure tests periodically can help identify leaks or integrity issues in the moisture separator. Additionally, adherence to manufacturer guidelines, proper installation, and regular maintenance practices are essential for safe operation.
If you encounter complex maintenance tasks or issues beyond your expertise, it's advisable to consult with a qualified technician or service provider specializing in compressed air and gas systems. They can provide professional diagnosis, repairs, and maintenance services as needed.