-
Call
-
Whatsapp
9825014048
-
Location
Blog
BLOG
Dry Screw Vacuum Pump
In many industrial applications, creating a vacuum is essential for processes ranging from material handling to chemical production. One of the most efficient and reliable ways to achieve this is through the use of a dry screw pump.
In this blog, we'll explore how dry screw vacuum pump work, their benefits, and why they are a popular choice in various industries.
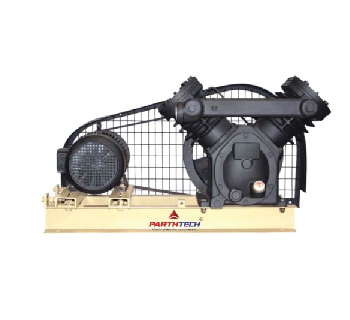
What is a Dry Screw Vacuum Pump?
No lubricant or sealing fluids are required inside the pumping chamber of a dry screw vacuum pump, which is a sort of positive shift pump that use two intermeshing screws to transfer gas through the pump. This "dry" operation makes these pumps ideal for applications where contamination by lubricants or fluids is unacceptable.
How Is a Dry Screw Vacuum Pump Operated?
1. Essential Components and Design:
A dry screw vacuum pump consists of two parallel screw rotors housed within a chamber. These screws rotate in opposite directions, and their precise, synchronized movement is critical to the pump's operation.
2. Gas Inlet:
The inlet port is where gas is admitted into the pump. As the screws rotate, they trap and move the gas along the length of the screws from the inlet to the outlet.
3. Compression and Transport:
The intermeshing screws create a series of chambers along their length. As the screws turn, these chambers move from the inlet towards the outlet, compressing the gas as it progresses. The tight tolerances between the screws and the chamber walls ensure efficient sealing and compression.
4. Gas Discharge:
Once the gas reaches the outlet port, it is expelled from the pump. Because the screws do not touch each other or the chamber walls, there is minimal wear, and the need for lubricants within the pumping chamber is eliminated.
5. Cooling and Heat Management:
Since there are no lubricants to absorb and dissipate heat, dry screw vacuum pumps often include external cooling systems to manage the heat generated during compression. This can involve air or water cooling mechanisms to maintain optimal operating temperatures.
Benefits of Dry Vacuum Pumps:
1. Oil-free Operation:
One of the most significant advantages of dry screw vacuum pumps is their oil-free operation. This makes them ideal for applications where contamination by oil or other fluids is unacceptable, such as in the pharmaceutical, food, and semiconductor industries.
2. High Efficiency and Performance:
Dry screw vacuum pumps are highly efficient, capable of achieving deep vacuum levels with consistent performance. Their design allows for a continuous gas flow with minimal pulsation, contributing to stable vacuum conditions.
3. Low Maintenance and Long Lifespan:
With no lubricants to change and minimal wear on moving parts, the maintenance requirements of dry screw vacuum pumps are lower than those of other vacuum pump types. Their robust design and durable components contribute to a long operational lifespan.
4. Versatility:
These pumps are versatile and can handle a wide range of gases, including those that are corrosive or contain particular matter. Because of this, they can be used in various industrial contexts, from chemical processing to packaging.
5. Environmentally Friendly:
By eliminating the need for lubricants and reducing the risk of contamination, dry screw vacuum pumps are an environmentally friendly option. They also tend to have lower energy consumption than other vacuum pump technologies.
Applications of Dry Screw Vacuum Pumps:
Dry Screw vacuum pumps are used in various industries and applications, including:
Chemical Processing: Handling and processing aggressive and corrosive gases.
Pharmaceuticals: Ensuring clean and contaminant-free vacuum environments for production processes.
Food Processing: Maintaining hygiene standards by avoiding oil contamination.
Semiconductor Manufacturing: Providing ultra-clean vacuum conditions critical for high-tech production.
Packaging: Ensuring efficient and contaminant-free packaging processes.
Conclusion:
Dry screw vacuum pumps are a reliable, efficient, and versatile solution for creating vacuum environments in a wide range of industrial applications. They are the best option for many vital processes due to their oil-free operation, excellent efficiency, cheap maintenance, and positive environmental impact. Understanding how these pumps work can help you appreciate their advantages and make informed decisions for your vacuum needs.
FAQs
Frequently Ask Questions
A positive displacement pump, known as a dry screw vacuum pump, does not require any sealing fluids or lubrication to transfer gas through the pump chamber; instead, it uses two intermeshing screws. This "dry" operation makes it ideal for applications where contamination by lubricants or fluids is unacceptable.
A dry screw vacuum pump works by using two parallel screw rotors that rotate in opposite directions. Gas enters the pump through the inlet, is trapped and compressed between the screws, and then expelled through the outlet. The screws do not touch each other or the chamber walls, eliminating the need for lubricants.
The main components of a dry screw vacuum pump include: 1) Two intermeshing screw rotors, 2) A housing chamber, 3) Gas inlet and outlet ports, 4) External cooling system (air or water).
The benefits of using a dry screw vacuum pump include: 1) Oil-free operation, preventing contamination, 2) High efficiency and performance with deep vacuum levels, 3) Low maintenance and long operational lifespan, 4) Versatility in handling various gases, including corrosive ones, 5) Environmentally friendly due to reduced lubricant use and lower energy consumption.
Dry screw vacuum pumps are commonly used in industries such as: 1) Chemical processing, 2) Pharmaceuticals, 3) Food processing, 4) Semiconductor manufacturing, 5) Packaging.
Dry screw vacuum pumps are environmentally friendly because they eliminate the need for lubricants within the pumping chamber, reducing the risk of contamination. They also tend to have lower energy consumption than other vacuum pump technologies.