-
Call
-
Whatsapp
9825014048
-
Location
Blog
BLOG
Double Stage Air Compressors
Many businesses rely on air compressors, providing a steady and reliable compressed air source for numerous applications. Double-stage air compressors have gained popularity for their enhanced efficiency and superior performance among the different types of air compressors. In this blog, we will dive into the advantages of double-stage air compressors and how they boost efficiency in diverse industrial settings.
Higher Pressure Ratios:
One of the primary advantages of double-air compressors is their ability to achieve higher pressure ratios compared to single-stage counterparts. These compressors can deliver compressed air at significantly higher pressures by dividing the compression process into two stages. This makes them well-suited for applications that demand elevated pressure levels, such as power generation, petrochemical plants, and heavy manufacturing.
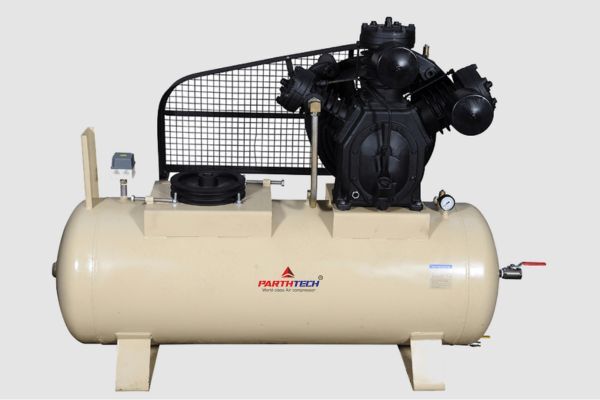
Improved Efficiency:
Double-stage air compressors are known for their improved overall efficiency. The compression process is divided into two stages, with intercooling between the stages. This intercooling helps reduce the heat generated during compression, making the process more energy-efficient. As a result, double-stage compressors consume less power per unit of compressed air produced, leading to cost savings in the long run.
Enhanced Cooling Mechanism:
Efficient cooling is essential to keep an air compressor running smoothly and for a long time. Double-stage compressors inherently benefit from an improved cooling mechanism due to the intercooler process between stages. This prevents the compressor from overheating, guaranteeing reliable operation while decreasing the likelihood of critical parts experiencing damage.
Suitability for High-Volume Applications:
Industries that require a continuous and high-volume supply of compressed air, such as those in the automotive and aerospace sectors, find double-stage compressors particularly advantageous. These compressors can handle large air volumes efficiently, meeting the demands of heavy-duty applications without compromising performance.
Reduced Moisture Content:
Compressed air containing moisture can cause corrosion, harm pneumatic tools, and lower product quality. Double-stage air compressors, with their intercooling feature, contribute to dehumidifying compressed air. This is especially beneficial for applications where dry and clean compressed air is crucial, such as pharmaceutical and food processing industries.
Flexibility in pressure adjustment:
Double-stage air compressors offer greater flexibility in adjusting pressure levels according to specific application requirements. This adaptability makes them suitable for various industries with varying pressure needs, providing a versatile solution for diverse manufacturing processes.
Conclusion:
In conclusion, industries that want to improve efficiency highly favour double-stage air compressors due to their many advantages, performance, and versatility in their compressed air systems. The ability to achieve higher pressure ratios improved overall efficiency and reduced moisture content, positioning double-stage air compressors as indispensable assets in various industrial applications, contributing to increased productivity and cost-effectiveness.
FAQs
Frequently Ask Questions
A double-stage air compressor is a type of air compressor that compresses air in two stages to achieve higher pressure ratios. The compression process is divided into two phases, with intercooling between them, resulting in improved efficiency and performance.
Intercooling involves cooling the air between the two compression stages, reducing the heat generated during compression. This improves efficiency by minimizing energy losses and allowing the compressor to operate more effectively.
Double-stage air compressors find applications in various industries, including power generation, petrochemical plants, automotive, aerospace, pharmaceuticals, food processing, and heavy manufacturing. Their ability to handle high pressure and volume makes them versatile for diverse industrial processes.
Higher pressure ratios make double-stage compressors suitable for applications that require elevated pressure levels. Industries with specific pressure demands, such as those dealing with heavy-duty manufacturing processes, benefit from the capability of double-stage compressors to deliver compressed air at higher pressures.
The intercooling process in double-stage compressors aids in reducing the moisture content in compressed air. This is crucial for applications where dry and clean compressed air is essential, preventing corrosion and damage to tools and ensuring the quality of end products.
Yes, double-stage air compressors are generally more energy-efficient. The intercooling between stages helps minimise energy losses during compression, improving overall efficiency. Over time, this energy efficiency can result in savings.
Double-stage air compressors offer flexibility in adjusting pressure levels according to specific application requirements. This adaptability makes them suitable for various industries with varying pressure needs, providing a versatile solution for different manufacturing processes.
Regular maintenance, including checking for leaks, monitoring cooling systems, and ensuring proper lubrication, is crucial for the optimal performance and longevity of double-stage air compressors. Following manufacturer recommendations for maintenance schedules is advisable.
Yes, double-stage air compressors are well-suited for industries requiring a continuous and high-volume supply of compressed air, such as automotive and aerospace. Their ability to handle large air volumes efficiently makes them ideal for heavy-duty applications.
Yes, the enhanced efficiency and lower energy consumption of double-stage air compressors can reduce operating costs over time. Although there may be a higher initial expenditure, many industries find them a cost-effective solution due to the long-term savings in energy usage.